Рабочие условия нефтеперерабатывающих заводов меняются, и такие перемены могут потребовать особого подхода к себе. В некоторых географических областях поменялись исторически сложившиеся поставщики сырой нефти, что привело к изменению состава сырой нефти. Метод транспортировки также может поменяться – с трубопровода, при стабильном составе, на транспортировку морскими судами, с различными составами.
Вне зависимости от этих изменений, качество конечного продукта нефтеперерабатывающих заводов должно быть стабильным, а количество производимого продукта должно только повышаться. В то же время воздействие производства на окружающую среду регулируется всё сильнее и сильнее, повышаются требования по мониторингу и отчётности. Выбросы нужно сокращать постоянно. В общем, от нефтепереработчиков требуется всё больше гибкости.
Всё это увеличивает нагрузку на установки производства серы, которые должны работать непрерывно и оптимизированно. Такие установки требуют особого внимания в плане безопасности и эксплуатационного мониторинга.
Сама по себе элементарная сера не представляет собой проблемы. Это один из самых распространённых элементов (по массе) на Земле. Сера играет важную роль в жизни на Земле. Сера присутствует в живых организмах, в том числе в людях, и может применяться для производства удобрений. Её даже применяют в медицине. Тем не менее, сера может быть вредной для человека и окружающей среды. Концентрации сероводорода (H2S) величиной всего лишь несколько частиц на миллион (ppm) в воздухе могут привести к заболеваниям, а при постоянном содержании выше 100 ppm – к смерти. Диоксид серы (SO2) токсичен для человека при очень низких концентрациях, но получил значительное внимание из-за своего негативного воздействия на экологию. Он может разрушать растительный и животный мир и вносит вклад в образование кислотных дождей.
Химические основы производства серы известны уже более 90 лет. В наше время производительность современных УПС может варьироваться от десятков до тысяч тонн производимой серы в сутки. Самый значительный прогресс был сделан в общей эффективности извлечения серы.
Хотя в 1970-х годах было достаточно поддерживать уровень эффективности извлечения серы на уровне 80-85%, а в 1990-х – 95-99%, то сейчас требование увеличилось до более чем 99,9%.
Учитывая, что нефтепереработчики используют те же химические основы, что и 90 лет назад, за исключением принципов, по которым работают установки очистки хвостовых газов, такое значительное улучшение эффективности возможно только благодаря эксплуатации надёжных контрольно-измерительных приборов (см. рисунок 1).
Вне зависимости от этих изменений, качество конечного продукта нефтеперерабатывающих заводов должно быть стабильным, а количество производимого продукта должно только повышаться. В то же время воздействие производства на окружающую среду регулируется всё сильнее и сильнее, повышаются требования по мониторингу и отчётности. Выбросы нужно сокращать постоянно. В общем, от нефтепереработчиков требуется всё больше гибкости.
Всё это увеличивает нагрузку на установки производства серы, которые должны работать непрерывно и оптимизированно. Такие установки требуют особого внимания в плане безопасности и эксплуатационного мониторинга.
Сама по себе элементарная сера не представляет собой проблемы. Это один из самых распространённых элементов (по массе) на Земле. Сера играет важную роль в жизни на Земле. Сера присутствует в живых организмах, в том числе в людях, и может применяться для производства удобрений. Её даже применяют в медицине. Тем не менее, сера может быть вредной для человека и окружающей среды. Концентрации сероводорода (H2S) величиной всего лишь несколько частиц на миллион (ppm) в воздухе могут привести к заболеваниям, а при постоянном содержании выше 100 ppm – к смерти. Диоксид серы (SO2) токсичен для человека при очень низких концентрациях, но получил значительное внимание из-за своего негативного воздействия на экологию. Он может разрушать растительный и животный мир и вносит вклад в образование кислотных дождей.
Химические основы производства серы известны уже более 90 лет. В наше время производительность современных УПС может варьироваться от десятков до тысяч тонн производимой серы в сутки. Самый значительный прогресс был сделан в общей эффективности извлечения серы.
Хотя в 1970-х годах было достаточно поддерживать уровень эффективности извлечения серы на уровне 80-85%, а в 1990-х – 95-99%, то сейчас требование увеличилось до более чем 99,9%.
Учитывая, что нефтепереработчики используют те же химические основы, что и 90 лет назад, за исключением принципов, по которым работают установки очистки хвостовых газов, такое значительное улучшение эффективности возможно только благодаря эксплуатации надёжных контрольно-измерительных приборов (см. рисунок 1).
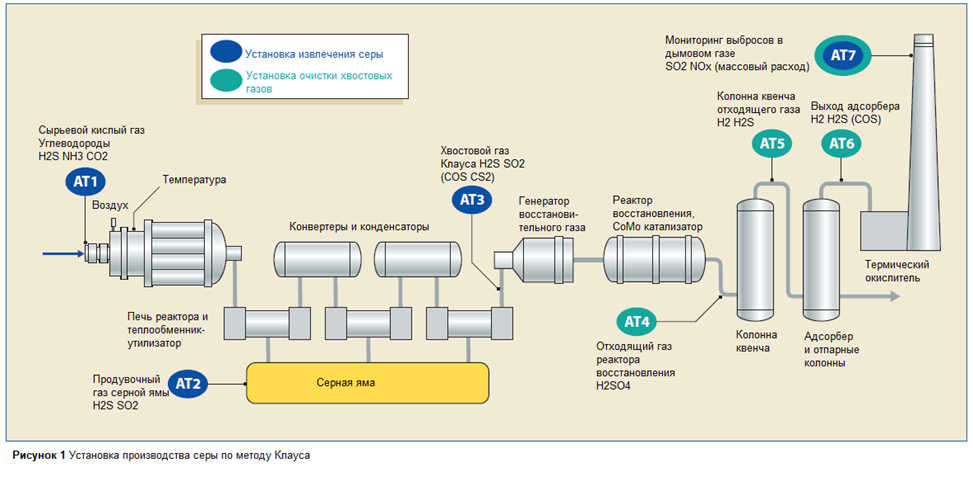
Далее перечислены основные задачи, которые необходимо решить:
• Понять экологическое воздействие каждого отдельного прибора
• Понять потенциальное улучшение, которое принесёт применение наилучшей комбинации приборов
• Научиться правильно применять приборы в рабочих условиях
• Смягчать нарушения условий работы с помощью понимания «неожиданного» поведения приборов
Представленный ниже обзор посвящён всем точкам отбора проб и их потенциальному влияния на экологию. При рассмотрении сырьевого газа АТ1 (см. рисунок 1), подаваемого в реакционную печь Клауса, где расположен анализатор сырьевого газа, можно сказать, что этот сырьевой газ (на нефтеперерабатывающих заводах) может состоять из двух потоков, идущих из разных источников. Первый – поток кислого газа, второй – газ из установки отпарки кислой воды.
Кислый газ обычно стабилен, тогда как газ из установки очистки кислой воды может являться потенциальным источником неполадок. При этом мы не должны считать, что кислый газ не может стать источником неполадок для УПС.
• Понять экологическое воздействие каждого отдельного прибора
• Понять потенциальное улучшение, которое принесёт применение наилучшей комбинации приборов
• Научиться правильно применять приборы в рабочих условиях
• Смягчать нарушения условий работы с помощью понимания «неожиданного» поведения приборов
Представленный ниже обзор посвящён всем точкам отбора проб и их потенциальному влияния на экологию. При рассмотрении сырьевого газа АТ1 (см. рисунок 1), подаваемого в реакционную печь Клауса, где расположен анализатор сырьевого газа, можно сказать, что этот сырьевой газ (на нефтеперерабатывающих заводах) может состоять из двух потоков, идущих из разных источников. Первый – поток кислого газа, второй – газ из установки отпарки кислой воды.
Кислый газ обычно стабилен, тогда как газ из установки очистки кислой воды может являться потенциальным источником неполадок. При этом мы не должны считать, что кислый газ не может стать источником неполадок для УПС.
Эксплуатационные условия нефтеперерабатывающего завода
Нефтепереработчикам необходимо эксплуатировать свои УПС одновременно на кислом газе и газе с установки очистки кислых вод. Это необязательное условие для всех установок или их ниток, но данный факт необходимо рассматривать как общее рабочее условие. Одну из проблем при работе с кислыми газами с установок очистки кислых стоков представляет собой аммиак (NH3), который входит в состав кислых стоков и требует работы реакционной печи Клауса при повышенной температуре (<1200C) для того, чтобы могла произойти реакция, и аммиак разложился перед попаданием в теплообменник.
Ключевой аспект любого измерения или контроля сырьевого газа – смягчение нарушения условий эксплуатации. Такие нарушения могут быть вызваны быстрыми изменениями содержания углеводородов в сырьевом газе. Такие изменения могут наблюдаться в обоих потоков – в кислом газе и в газе установки очистки кислых стоков. Углеводородам необходимо значительно большее количество кислорода (О2), чем сероводороду, для реакции в печи Клауса, как показано в таблице 1.
Ключевой аспект любого измерения или контроля сырьевого газа – смягчение нарушения условий эксплуатации. Такие нарушения могут быть вызваны быстрыми изменениями содержания углеводородов в сырьевом газе. Такие изменения могут наблюдаться в обоих потоков – в кислом газе и в газе установки очистки кислых стоков. Углеводородам необходимо значительно большее количество кислорода (О2), чем сероводороду, для реакции в печи Клауса, как показано в таблице 1.
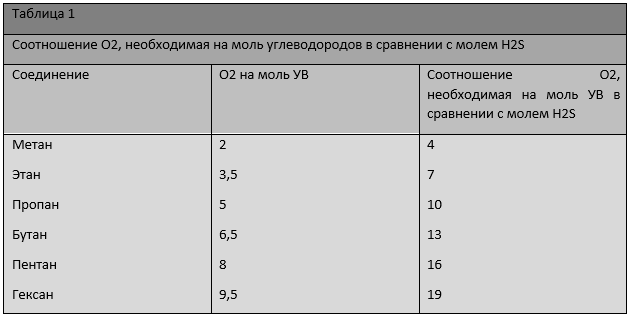
В зависимости от типа УПС неожиданное появление (или неожиданное исчезновение) углеводородов может привести к нарушениям рабочего режима. Потенциально такое воздействие может привести к тому, что придётся пропускать технологические этапы, что приведёт к потенциально существенным последствиям. В случае, если происходит байпас только установки очистки хвостовых газов, общий выброс диоксида серы (SO2) может увеличиться на два порядка. Нормальная концентрация SO2 после финального сжигания в комбинации с установкой очистки хвостовых газов составляет 200-400 ppm об SO2, что увеличится до 10 000/20 000 ppm об при байпасе установки очистки хвостовых газов.
Даже без осмысления таких исключительных рабочих условий можно сказать, что закрытый контур контроля сырьевого газа может сократить выброс на 10-15% от общего размера выбросов. Частота случаев вспышек на факеле может быть сокращена на 65-95%. Учитывая, что источником нарушений процесса, связанных с углеводородами, появляются выше по потоку от УПС, другой новой проблемой может стать частое изменение состава сырой нефти, а большинство нефтеперерабатывающих заводов к таким переменам не готово.
Надёжное определение состава сырьевого газа (H2S, NH3, общие углеводороды, CO2) сделают контроль процесса более эффективным. Быстрое реагирование на изменения в составе позволят быстро регулировать соотношение кислого газа к воздуху, что позволит сократить общий объём выбросов.
Серный отстойник АТ2 – мера предосторожности, где концентрация H2S должна поддерживаться ниже предела взрывоопасности (нижний предел взрывоопасности – 3,25 %об). SO2 следует измерять для того, чтобы предупредить возгорание серы.
Тлеющее горения серы не является чем-то из ряда вон выходящим; железные трубы вступают в реакцию с серой из пиритов, что представляет собой медленную, но экзотермическую реакцию, которая может стать источником возгорания. Например, с H2S в качестве источника топлива и пирофорным горением в качестве источника возгорания, третьей необходимой силой для возникновения огня является кислород.
В зоне анализатора хвостового газа АТ3, также известном как анализатор потребности в воздухе, от этого измерения зависит весь процесс контроля за модифицированным процессом Клауса. Главные компоненты, которые здесь нужно измерять, это H2S и SO2. Их компоненты могут представлять интерес, но не требуют контроля. Кстати, что собой представляет процесс контроля модифицированного процесса Клауса? Процесс состоит из двух этапов-химических реакций:
3H2S + 3/2O2 → SO2 + 2H2S + H2O
SO2 + 2H2S ↔ 3Sx + 2H2O
Первое – термическая реакция (печь Клауса), за которой следует каталитическая реакция. Ключевой параметр – расход воздуха (кислорода) в термический реактор. Его конфигурация приведёт к определённому отношению H2S:SO2. Для модифицированной установки Клауса данное соотношение описывается как 2:1. В зависимости от установки очистки хвостовых газов ниже по потоку от установки Клауса, данное соотношение может отличаться.
Как показано на рисунке 2, анализатор хвостового газа контролирует клапан регулировочного воздуха, который обычно составляет 10% от потока воздуха в реакционную печь. Клапан основного воздуха устанавливается на соотношение кислый газ к воздуху на основе наиболее проверенной информации о газе, поступающем в реактор. Это возвращает нас к предыдущим аргументам: улучшенный контроль процесса благодаря надёжному анализу состава сырьевого газа. Два измерения (сырьевой и хвостовой газы) вместе позволят добиться повышенного контроля процесса.
Даже без осмысления таких исключительных рабочих условий можно сказать, что закрытый контур контроля сырьевого газа может сократить выброс на 10-15% от общего размера выбросов. Частота случаев вспышек на факеле может быть сокращена на 65-95%. Учитывая, что источником нарушений процесса, связанных с углеводородами, появляются выше по потоку от УПС, другой новой проблемой может стать частое изменение состава сырой нефти, а большинство нефтеперерабатывающих заводов к таким переменам не готово.
Надёжное определение состава сырьевого газа (H2S, NH3, общие углеводороды, CO2) сделают контроль процесса более эффективным. Быстрое реагирование на изменения в составе позволят быстро регулировать соотношение кислого газа к воздуху, что позволит сократить общий объём выбросов.
Серный отстойник АТ2 – мера предосторожности, где концентрация H2S должна поддерживаться ниже предела взрывоопасности (нижний предел взрывоопасности – 3,25 %об). SO2 следует измерять для того, чтобы предупредить возгорание серы.
Тлеющее горения серы не является чем-то из ряда вон выходящим; железные трубы вступают в реакцию с серой из пиритов, что представляет собой медленную, но экзотермическую реакцию, которая может стать источником возгорания. Например, с H2S в качестве источника топлива и пирофорным горением в качестве источника возгорания, третьей необходимой силой для возникновения огня является кислород.
В зоне анализатора хвостового газа АТ3, также известном как анализатор потребности в воздухе, от этого измерения зависит весь процесс контроля за модифицированным процессом Клауса. Главные компоненты, которые здесь нужно измерять, это H2S и SO2. Их компоненты могут представлять интерес, но не требуют контроля. Кстати, что собой представляет процесс контроля модифицированного процесса Клауса? Процесс состоит из двух этапов-химических реакций:
3H2S + 3/2O2 → SO2 + 2H2S + H2O
SO2 + 2H2S ↔ 3Sx + 2H2O
Первое – термическая реакция (печь Клауса), за которой следует каталитическая реакция. Ключевой параметр – расход воздуха (кислорода) в термический реактор. Его конфигурация приведёт к определённому отношению H2S:SO2. Для модифицированной установки Клауса данное соотношение описывается как 2:1. В зависимости от установки очистки хвостовых газов ниже по потоку от установки Клауса, данное соотношение может отличаться.
Как показано на рисунке 2, анализатор хвостового газа контролирует клапан регулировочного воздуха, который обычно составляет 10% от потока воздуха в реакционную печь. Клапан основного воздуха устанавливается на соотношение кислый газ к воздуху на основе наиболее проверенной информации о газе, поступающем в реактор. Это возвращает нас к предыдущим аргументам: улучшенный контроль процесса благодаря надёжному анализу состава сырьевого газа. Два измерения (сырьевой и хвостовой газы) вместе позволят добиться повышенного контроля процесса.
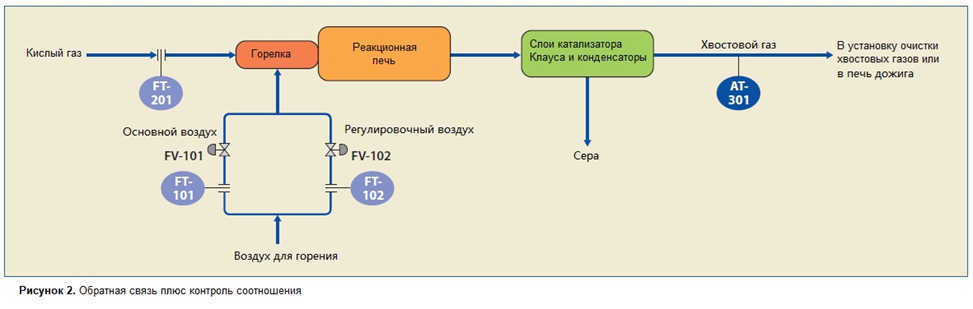
Контроль модифицированной установки Клауса
Необходимо понимать потенциальное влияние на схему контроля процесса каждого из установленных измерительных приборов. Принцип «пусть будет» не работает; необходимо, чтобы приборы работали надежно и безопасно. Значительные улучшения уровня извлечения серы в модифицированной установке Клауса возможны благодаря современному измерительному оборудованию и комбинированию их в единую схему контроля всего процесса.
Важно, чтобы любое измерительное оборудование, помимо безопасности, предоставляло быстрые и надёжные данные. Простой неприемлем.
На сегодняшний день законы не позволяют иметь уровень извлечения серы на производстве менее 99%. Выбросы серы в любом случае будут слишком высоки. Одна только модифицированная установка Клауса не позволит достичь необходимого уровня конверсии серы. Таким образом, необходимо устанавливать установку очистки хвостовых газов ниже по потоку. Чаще всего сейчас устанавливают установки на аминовой основе.
Цель установки очистки хвостовых газов – конвертировать все оставшиеся сернистые компоненты, которые приходят с модифицированной установки Клауса, в H2S. Эта конверсия происходит в каталитической секции процесса очистки хвостовых газов. В восстановительном реакторе применяется кобальт-молибденовый (CoMo) катализатор. Реакции, катализаторами которых являются кобальт и молибден, показаны на рисунке 3.
Важно, чтобы любое измерительное оборудование, помимо безопасности, предоставляло быстрые и надёжные данные. Простой неприемлем.
На сегодняшний день законы не позволяют иметь уровень извлечения серы на производстве менее 99%. Выбросы серы в любом случае будут слишком высоки. Одна только модифицированная установка Клауса не позволит достичь необходимого уровня конверсии серы. Таким образом, необходимо устанавливать установку очистки хвостовых газов ниже по потоку. Чаще всего сейчас устанавливают установки на аминовой основе.
Цель установки очистки хвостовых газов – конвертировать все оставшиеся сернистые компоненты, которые приходят с модифицированной установки Клауса, в H2S. Эта конверсия происходит в каталитической секции процесса очистки хвостовых газов. В восстановительном реакторе применяется кобальт-молибденовый (CoMo) катализатор. Реакции, катализаторами которых являются кобальт и молибден, показаны на рисунке 3.
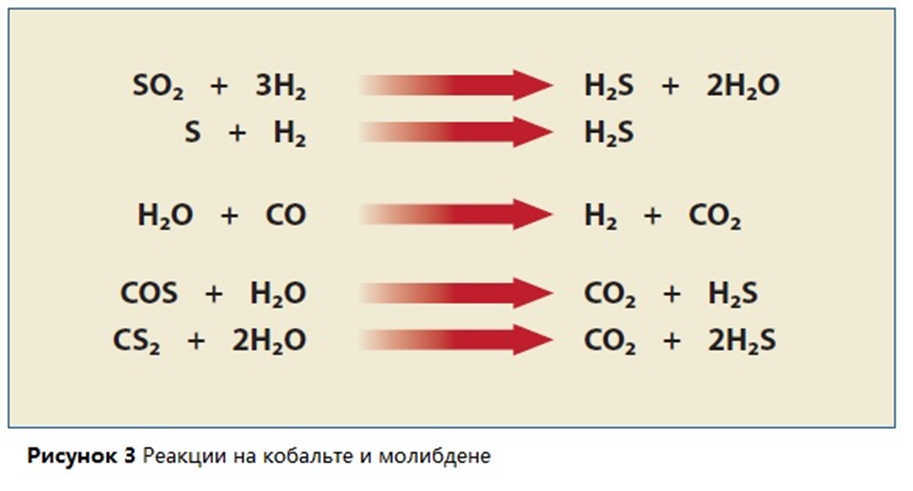
Первый этап реакции требует наличия водорода (Н2). Н2 может присутствовать в качестве побочного продукта модифицированной реакции Клауса, но также может быть выработан поточной восстановительной горелкой или подан из внешнего источника. Для того, чтобы обеспечить полную реакцию «сернистых соединений в H2S», необходимо избыточное количество Н2 после восстановительного реактора, вне зависимости от источника Н2.
На втором этапе процесса необходимо сепарировать H2S и вернуть его на вход печи модифицированной установки Клауса. Данный этап основан на системе аминовой адсорбции и регенерации.
Требуемая и прогнозируемая общая эффективность извлечения серы (модифицированной установки Клауса и установки очистки хвостовых газов) составляет более 99,9%. Это подтверждается измерением общего массового выброса диоксида серы (SO2) на выходе из последнего термического реактора, или «дымовой трубы». Два объекта, которые необходимо тщательно контролировать, - колонна квенча и выход адсорбера.
Что касается измерения на выходе из колонны квенча АТ5 (Н2 и H2S), с тех пор, как процесс очистки хвостовых газов был впервые представлен в виде SCOT (Shell Claus Off-Gas Treating), на данном этапе ожидается проведение измерения Н2. Оно было включено в оригинальный дизайн системы. Как ранее упоминалось, цель измерения Н2 здесь это удостовериться, что из СоМо реактора выходит избыточный Н2.
Также в этой точке измеряется H2S, чтобы операторы и автоматическая система контроля понимали, какое количество H2S поступит в адсорбер.
Анализ образцов газа в этой точке процесса проще для отбора, чем измерения АТ4 на входе в колонну квенча, так как температура технологического газа ниже. Любые частицы также будут удалены в колонне квенча.
Изначально измерение АТ6 на выходе из адсорбера было определено как только измерение H2S для определения производительности аминового адсорбера. В результате совершенствования знания о процессе и появления мультикомпонентных измерительных приборов, появился интерес к дополнительным измерениям.
Осознавая важность избыточного Н2 в установке очистки хвостовых газов и понимая, что анализатор существенно не подорожает, если к нему добавить один дополнительный компонент измерения, вы можете добавить на этой точке измерение избыточного Н2. Добавив измерение Н2, его избыточность будет достигаться без лишних затрат.
То же самое можно сказать про добавление измерений COS и/или CS2; оба показателя можно применять для оценки состояния СоМо катализатора. Если показатели COS и CS2 повышаются, то СоМо катализатор следует менять, или следует регулировать другие эксплуатационные переменные, такие как расход или температура, или следует обратить внимание на модифицированный процесс Клауса, где могут быть некие эксплуатационные проблемы.
Оглядываясь на комбинацию двух ранее описанных точек отбора проб, можно сказать, что дополнительное измерение Н2 обеспечит оптимальную производительность установки очистки хвостовых газов. Оно позволит сократить затраты на замену загрязненного амина и минимизировать простой установки.
Если H2S измеряется на выходе из колонны квенча и на выходе из адсорбера, то эффективность адсорбера можно будет оценивать и контролировать онлайн круглосуточно. Контроль рециклинга/регенерации амина также возможен на основе измерения входного и выходного показателей H2S.
Финальный параметр контроля качества – массовый выброс SO2, его необходимо измерять на выходе из термического окислителя. Только массовый выброс может показать истинный уровень извлечения серы. Точное значение позволит получить сочетание показателей H2S, подаваемого в процесс, и количество SO2, покидающего окислитель.
На втором этапе процесса необходимо сепарировать H2S и вернуть его на вход печи модифицированной установки Клауса. Данный этап основан на системе аминовой адсорбции и регенерации.
Требуемая и прогнозируемая общая эффективность извлечения серы (модифицированной установки Клауса и установки очистки хвостовых газов) составляет более 99,9%. Это подтверждается измерением общего массового выброса диоксида серы (SO2) на выходе из последнего термического реактора, или «дымовой трубы». Два объекта, которые необходимо тщательно контролировать, - колонна квенча и выход адсорбера.
Что касается измерения на выходе из колонны квенча АТ5 (Н2 и H2S), с тех пор, как процесс очистки хвостовых газов был впервые представлен в виде SCOT (Shell Claus Off-Gas Treating), на данном этапе ожидается проведение измерения Н2. Оно было включено в оригинальный дизайн системы. Как ранее упоминалось, цель измерения Н2 здесь это удостовериться, что из СоМо реактора выходит избыточный Н2.
Также в этой точке измеряется H2S, чтобы операторы и автоматическая система контроля понимали, какое количество H2S поступит в адсорбер.
Анализ образцов газа в этой точке процесса проще для отбора, чем измерения АТ4 на входе в колонну квенча, так как температура технологического газа ниже. Любые частицы также будут удалены в колонне квенча.
Изначально измерение АТ6 на выходе из адсорбера было определено как только измерение H2S для определения производительности аминового адсорбера. В результате совершенствования знания о процессе и появления мультикомпонентных измерительных приборов, появился интерес к дополнительным измерениям.
Осознавая важность избыточного Н2 в установке очистки хвостовых газов и понимая, что анализатор существенно не подорожает, если к нему добавить один дополнительный компонент измерения, вы можете добавить на этой точке измерение избыточного Н2. Добавив измерение Н2, его избыточность будет достигаться без лишних затрат.
То же самое можно сказать про добавление измерений COS и/или CS2; оба показателя можно применять для оценки состояния СоМо катализатора. Если показатели COS и CS2 повышаются, то СоМо катализатор следует менять, или следует регулировать другие эксплуатационные переменные, такие как расход или температура, или следует обратить внимание на модифицированный процесс Клауса, где могут быть некие эксплуатационные проблемы.
Оглядываясь на комбинацию двух ранее описанных точек отбора проб, можно сказать, что дополнительное измерение Н2 обеспечит оптимальную производительность установки очистки хвостовых газов. Оно позволит сократить затраты на замену загрязненного амина и минимизировать простой установки.
Если H2S измеряется на выходе из колонны квенча и на выходе из адсорбера, то эффективность адсорбера можно будет оценивать и контролировать онлайн круглосуточно. Контроль рециклинга/регенерации амина также возможен на основе измерения входного и выходного показателей H2S.
Финальный параметр контроля качества – массовый выброс SO2, его необходимо измерять на выходе из термического окислителя. Только массовый выброс может показать истинный уровень извлечения серы. Точное значение позволит получить сочетание показателей H2S, подаваемого в процесс, и количество SO2, покидающего окислитель.
Заключение
Современное контрольно-измерительное оборудование позволяет сократить выбросы УПС.
Изначальные инвестиции не малы, но задачи, которые ставит данный процесс, сложны в плане надёжности и безопасности (УПС работает с самой токсичной смесью газов на всём нефтеперерабатывающем заводе). Знание, понимание и тренинги – ключевые факторы в работе с контрольно-измерительным оборудованием; без данных контрольно-измерительных приборов целевые показатели выбросов недостижимы.
Для достижения производственных целей различные технические дисциплины должны работать вместе еще на базе проектирования установок. Недостаточность знаний о трубопроводах может привести к тому, что оборудования будет недостаточно безопасным.
Если вы выберете «неподходящее» контрольно-измерительное оборудование, то лучшая возможная производительность процесса может не быть достигнута. Если персонал будет недостаточно квалифицированным, то контрольно-измерительное оборудование будет эксплуатироваться не так как должно. Наконец, средний срок службы приборов, установленных в УПС, составляет 15-20 лет. В таких условиях может быть непросто выбрать подходящего поставщика.
Йохен Гейгер, Майкл Гаура и Ананта Куккувада
AMETEK Process Instruments
На материале www.digitalrefining.com
Изначальные инвестиции не малы, но задачи, которые ставит данный процесс, сложны в плане надёжности и безопасности (УПС работает с самой токсичной смесью газов на всём нефтеперерабатывающем заводе). Знание, понимание и тренинги – ключевые факторы в работе с контрольно-измерительным оборудованием; без данных контрольно-измерительных приборов целевые показатели выбросов недостижимы.
Для достижения производственных целей различные технические дисциплины должны работать вместе еще на базе проектирования установок. Недостаточность знаний о трубопроводах может привести к тому, что оборудования будет недостаточно безопасным.
Если вы выберете «неподходящее» контрольно-измерительное оборудование, то лучшая возможная производительность процесса может не быть достигнута. Если персонал будет недостаточно квалифицированным, то контрольно-измерительное оборудование будет эксплуатироваться не так как должно. Наконец, средний срок службы приборов, установленных в УПС, составляет 15-20 лет. В таких условиях может быть непросто выбрать подходящего поставщика.
Йохен Гейгер, Майкл Гаура и Ананта Куккувада
AMETEK Process Instruments
На материале www.digitalrefining.com